Tailoring Solution Accuracy for Fast Whole-body Model Predictive Control of Legged Robots
Motivation
Legged robots have great potential for applications requiring animal-like mobility, but they are difficult to control. Non-linear model predictive control (NMPC) is a powerful tool for providing closed-loop stability to constrained non-linear systems. It uses a model to rapidly design new behaviors via online optimization. Yet, achieving real-time rates for high-dimensional systems like legged robots is challenging, especially when aiming for highly accurate optimal solutions with inequality constraints. However, real robotic systems may not always benefit from high-accuracy solutions due to modeling errors and delays. We present an implementation of whole-body NMPC with inequality constraints. We found that using low-accuracy solutions at rapid rates outperforms high-accuracy solutions at slower rates. We demonstrate our approach through extensive simulation and hardware walking experiments on the MIT Humanoid.
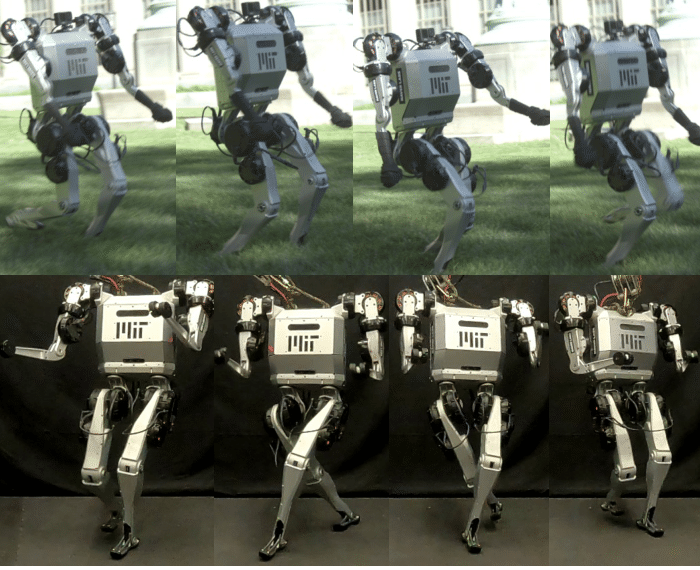
Hardware Demonstration
We demonstrate our approach on the MIT Humanoid. A video of our extensive hardware walking experiments can be found below:
Publications
This work is published in the IEEE Robotics and Automation Letters. The paper preprint can be accessed at https://arxiv.org/abs/2407.10789 .
Abstract
Thanks to recent advancements in accelerating non-linear model predictive control (NMPC), it is now feasible to deploy whole-body NMPC at real-time rates for humanoid robots. However, enforcing inequality constraints in real time for such high-dimensional systems remains challenging due to the need for additional iterations. This paper presents an implementation of whole-body NMPC for legged robots that provides low-accuracy solutions to NMPC with general equality and inequality constraints. Instead of aiming for highly accurate optimal solutions, we leverage the alternating direction method of multipliers to rapidly provide low-accuracy solutions to quadratic programming subproblems. Our extensive simulation results indicate that real robots often cannot benefit from highly accurate solutions due to dynamics discretization errors, inertial modeling errors and delays. We incorporate control barrier functions (CBFs) at the initial timestep of the NMPC for the self-collision constraints, resulting in up to a 26-fold reduction in the number of self-collisions without adding computational burden. The controller is reliably deployed on hardware at 90 Hz for a problem involving 32 timesteps, 2004 variables, and 3768 constraints. The NMPC delivers sufficiently accurate solutions, enabling the MIT Humanoid to plan complex crossed-leg and arm motions that enhance stability when walking and recovering from significant disturbances.